|
Post by Big D on Nov 1, 2014 14:32:15 GMT -7
I was asked to post some pictures of my knife work. I made hunting knives,kitchen knives, and collector knives for 20 years. I always wanted to make custom automatic knives, or switchblades, but they are very,very hard to make and nobody to teach you. Then quite by accident I met a world renown very famous [ in the knife world ] custom SB maker by the name of Don "Merlin" Hall. I had heard of him but never dreamed I would ever meet him. When he learned of my desire to do what he was doing he invited me to come to his home and work with him in his shop and he would teach me his craft. I dropped everything and went to his home in Miss. and lived with him and his family for a month and then went back for a couple of weeks every year trying to perfect me craft. We became best friends and his family were wonderful. His wife is a gourmet cook and boy did I eat good! I made custom Switchblades the last 10 yrs. of my career. I'm trying to make this short but one thing I have to mention, I never thought I could the fancy filework and all that would always be beyond my artistic abilities. When I told Don he said "BS" and started teaching me how to do it. I found I actually had a knack for it and did real well with it. I have always felt I wasn't artistic that way so I was always proud I could do it. I hope you enjoy these pictires. Many years of hard work and building up from a Black & Decker drill grinder to a large shop with $3,000.00 grinders. This is a pic of the four knives I am going to post. 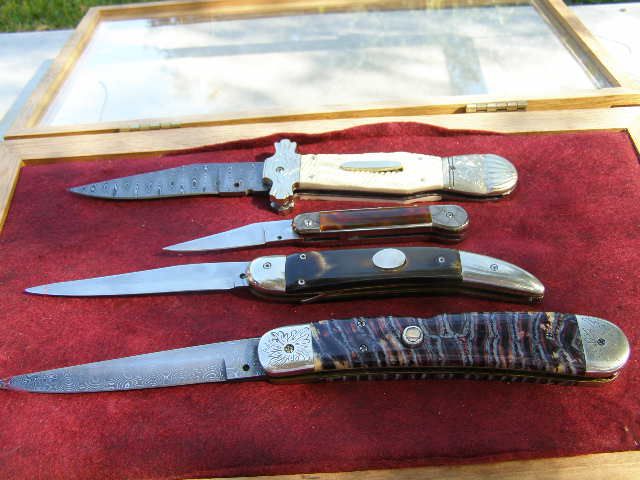
|
|
|
Post by Big D on Nov 1, 2014 14:47:36 GMT -7
|
|
|
Post by Big D on Nov 1, 2014 14:52:08 GMT -7
This second one was made for my wife. It has tortoise shell handles and Mokume bolsters which I heat treated to get the gold and purple color. Blade is 1070 high carbon steel. The thing on this knife is the whole handle is the button. 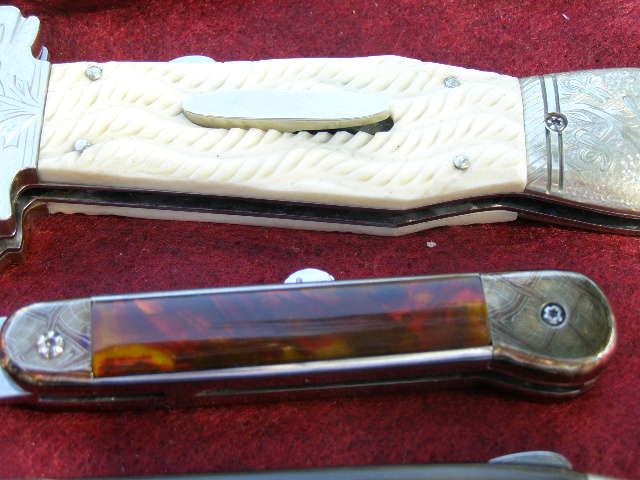 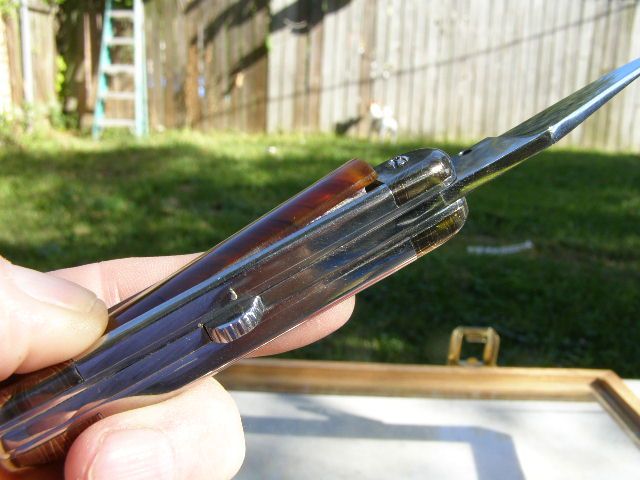
|
|
|
Post by Big D on Nov 1, 2014 15:04:32 GMT -7
|
|
|
Post by Big D on Nov 1, 2014 15:24:06 GMT -7
This last one is my masterpiece. This knife is massive. 12" long and 1 3/4" wide. Blade is 1/4" thick 350 layer hand forged Damascus steel. Back spring and kick spring are also Damascus steel. Engraved nickel silver bolsters. I inlaid the bolsters with 24k gold but it is hard to see. The handles are 20,000 year old Wholly Mammoth Tooth! One tooth from one of these creatures is the size of a large medicine ball. In all 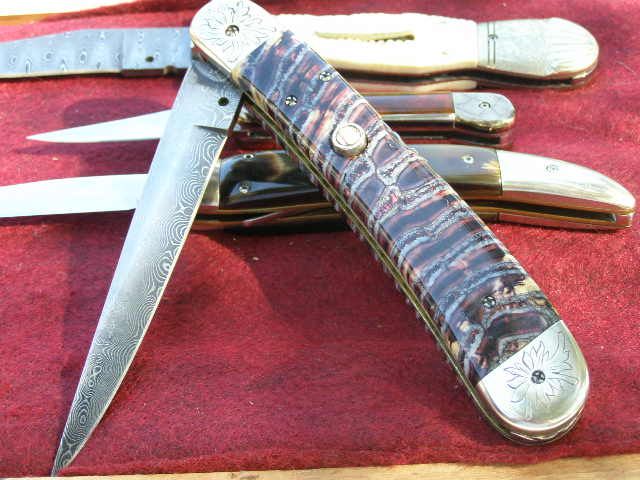 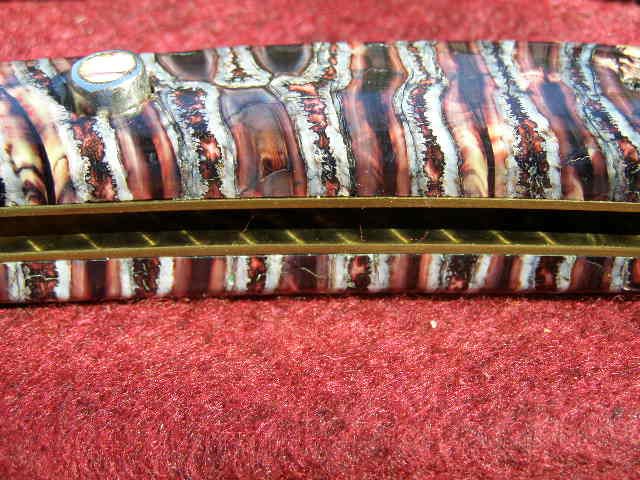 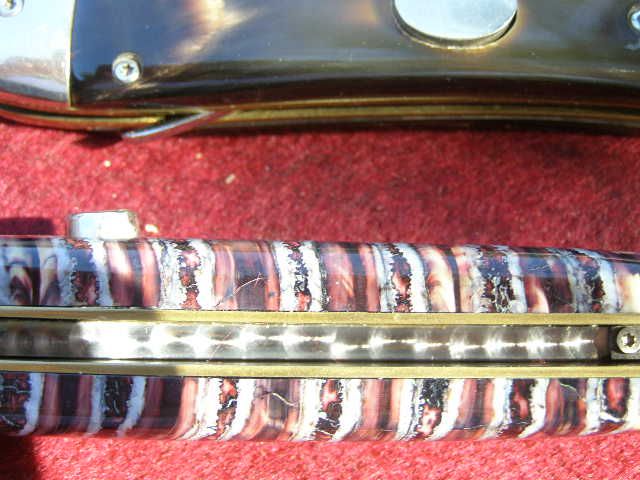 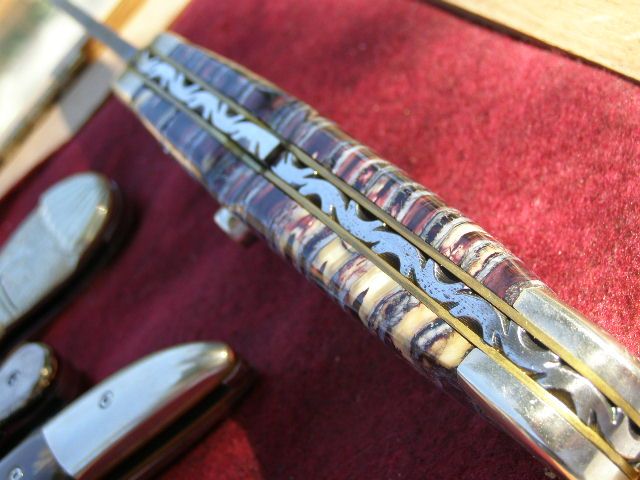 the years I used this stuff I never saw any this color. Beautiful! Most are blue and silver in color. This is the natural fossilized color that it 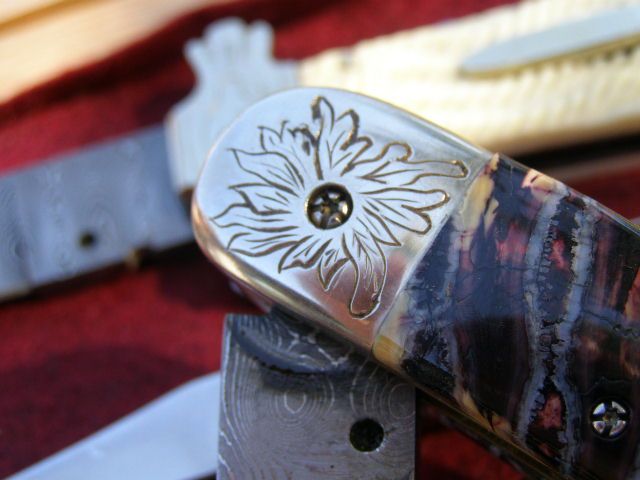 comes out of the ground with. Button is drilled nickel silver inlaid with tooth. This knife fires like a rocket and will really rock you when you push the button. This knife is my own design and I won many awards with it. Firing spring is jeweled and the brass liners are also jeweled.  Since you can't see any name stamp and you might wonder if these are really mine, I never mar the blade with a name stamp. I engrave my name 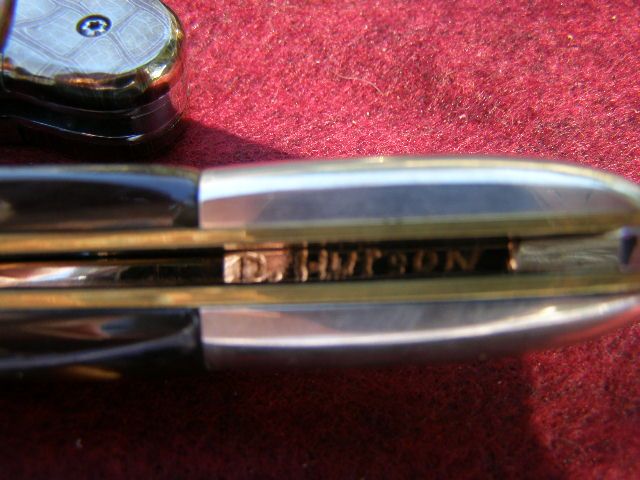 on the inside. Pics of my name also included.
|
|
Deleted
Registered: Nov 30, 2024 18:11:41 GMT -7
Posts: 0
|
Post by Deleted on Nov 1, 2014 16:01:00 GMT -7
WOW mate , they are some very impressive knives , a lot of skill involved there. I really like the colors in the mammoth toothed one especially. An absolute credit to you Dennis.
|
|
|
Post by sharp on Nov 1, 2014 21:28:13 GMT -7
very nice looking knives Dennis!
|
|
|
Post by Skip-O-Matic on Nov 2, 2014 21:01:00 GMT -7
Those are some beautiful knives. You sir are a craftsman.
|
|
|
Post by Big D on Nov 2, 2014 21:12:54 GMT -7
Thank you so much DeeCee,Sharp and Skip. These are, of course, just a very small sample of the hundreds I made over the years. Lot of blood,sweat,tears and love in them. I'm so glad you liked them. The Mammoth tooth knife cost $1,000.00 to make and sold for 3,000.00 and took 60 hours to build. Everything in all these knives was made from scratch.
|
|
|
Post by jbailey on Nov 2, 2014 21:24:08 GMT -7
Very cool knives Dennis! I've always wanted a Damascus steel bladed knife, just something about the pattern that I really enjoy. Great craftsmanship here bud!
|
|
|
Post by Big D on Nov 2, 2014 23:04:21 GMT -7
Thank You JB. I used Chad Nichols Damascus. I used to go to his shop in Miss. when he was just starting to catch on and now he makes for Buck and Case knife Co's. You know Damascus is like snow flakes no two ever have the same pattern.
|
|
Deleted
Registered: Nov 30, 2024 18:11:41 GMT -7
Posts: 0
|
Post by Deleted on Nov 3, 2014 7:07:57 GMT -7
-All i can say is..... HOLY strawberry!
WOW! I can not imagine the grinding you had have to do to get the blades to look like that 3rd or 4th one down.... DAMN!
This kinda stuff reminds me of work I done not much over 2 years ago! Simply, speechless Dennis, and THAT NEVER happens with me!
|
|
Deleted
Registered: Nov 30, 2024 18:11:41 GMT -7
Posts: 0
|
Post by Deleted on Nov 3, 2014 15:45:39 GMT -7
wow! those are some fine lookin blades Dennis!
|
|
|
Post by Big D on Nov 3, 2014 16:11:28 GMT -7
Thank you Knarf. I appreciate you taking the time to look at them and I'm really glad you liked them.
|
|
Deleted
Registered: Nov 30, 2024 18:11:41 GMT -7
Posts: 0
|
Post by Deleted on Nov 3, 2014 17:06:01 GMT -7
-I'm sorry, I miss lead ya! Same knife tho, but the blade I was referring too is this one: 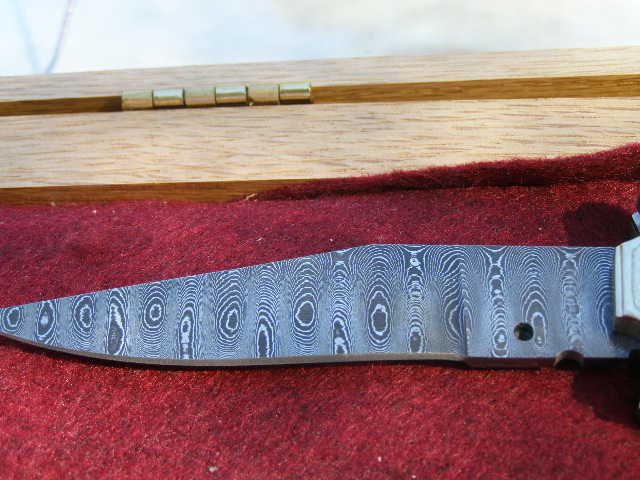 DAMN that looks AWESOME, NICE work............. Question the wood grain "look" ground in or etched? (I almost feel as tho I ought to know this one!) BUT, because I don't, I have to ask!
|
|
|
Post by jbailey on Nov 3, 2014 18:04:48 GMT -7
John, I'm sure Dennis could explain this better, but from what I was told many years ago they get that look by forging the steel and folding it over many many times and then when you section it it looks like the blade you quoted. It is called Damascus steel and is quite cool looking.
|
|
|
Post by Big D on Nov 3, 2014 18:07:59 GMT -7
You still got it right John, the same steel is in the last knife also. The etched pattern is in the steel. 350 layers of high carbon steel, very thin, are bound together and placed in a furnace and then placed under a giant hammer which rises and falls until the plates are all welded together. The pattern is formed during this process and no two are ever alike. Some hand makers who forge their own blades do this process on a small scale by forging plates in a small furnace and welding them together with a small sledge hammer.
|
|
Deleted
Registered: Nov 30, 2024 18:11:41 GMT -7
Posts: 0
|
Post by Deleted on Nov 3, 2014 23:28:51 GMT -7
Gawd thats a lot of work and skill into one small area! WOW!
I'm still on that "Holy strawberry" mode......WOW!
|
|
Deleted
Registered: Nov 30, 2024 18:11:41 GMT -7
Posts: 0
|
Post by Deleted on Sept 3, 2015 16:54:59 GMT -7
Nice autos ! Love the vine file work. I was never able to get the hang of that with out boogering up the back springs. Beautiful damascus steel too. I don't think I've ever seen mammoth look like that, but wow !! (those scales must have cost a fortune, I would have been too scared to work them) I like that you used the screws instead of peening, makes maintenance a lot easier especially for an auto. Very impressive work indeed !! As I mentioned, all I ever did was re-build and customize knives, mostly TL-29's into single blade jacks. Heres one from the old forums I used to haunt. www.allaboutpocketknives.com/knife_forum/viewtopic.php?f=14&t=41787I do miss working on knives, but blood thinners kind of stopped that. And besides, my wife's happy the house doesn't stink of bone dust anymore !!
|
|
|
Post by Big D on Sept 5, 2015 4:43:09 GMT -7
Nice autos ! Love the vine file work. I was never able to get the hang of that with out boogering up the back springs. Beautiful damascus steel too. I don't think I've ever seen mammoth look like that, but wow !! (those scales must have cost a fortune, I would have been too scared to work them) I like that you used the screws instead of peening, makes maintenance a lot easier especially for an auto. Very impressive work indeed !! As I mentioned, all I ever did was re-build and customize knives, mostly TL-29's into single blade jacks. Heres one from the old forums I used to haunt. www.allaboutpocketknives.com/knife_forum/viewtopic.php?f=14&t=41787I do miss working on knives, but blood thinners kind of stopped that. And besides, my wife's happy the house doesn't stink of bone dust anymore !! You did a good job on the Jack. Nice fit and finish. What did you use to jig it with and what did you stain it with? I made hunting, skinning, and kitchen knives for 20 yrs. before I started making autos. Whole different ballgame there. I've done many, many restorations on many types of knives. I got into restoring pocket knives once, which is a lost art and I never would have dreamed so many people had pocket knives they wanted restored. I could have given up everything else and just restored pocket knives for people and made a good living. I won a lot of awards with the Mammoth tooth knife. I never saw another set of Mammoth tooth scales that color and neither had anybody else I talked to. I got it from the Mammoth mines in Siberia. I have seen that stuff in great piles. I could talk knife work all day.
|
|
Deleted
Registered: Nov 30, 2024 18:11:41 GMT -7
Posts: 0
|
Post by Deleted on Sept 5, 2015 7:22:35 GMT -7
I can't take any credit for the scales. That's green bone - worm grooved , stained, and cut by Culppeper from their illustrious "clearance" page lol ! Think I paid $9.99 for that pair. I used to get all my handle material from them out of the bargain bin.
I regard you as an artisan, whereas myself, I would be more of a Frankenstein ! running-around-smiley-emoticon I got pretty good at taking beaters and making them useful again, but I wouldn't dare try to make money off it. I still have all my customs, since I never marked my work I didn't want anything winding up on eBay being misrepresented. Besides they got enough problems with all the Case forgeries that show up on there as it is.
|
|